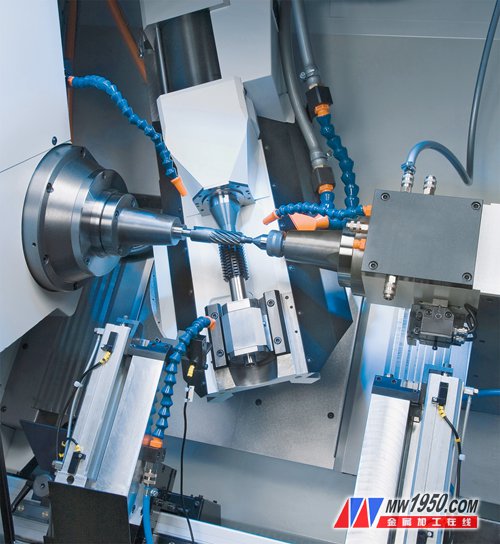
The K160 gear hobbing machine is machining the steering gear: the gear machining can be completed in only 15-20 seconds. When machining one steering gear, the other workpiece is placed in advance at the loading position without affecting the machining time. This unloading technology concept can achieve such incredibly fast machining time.
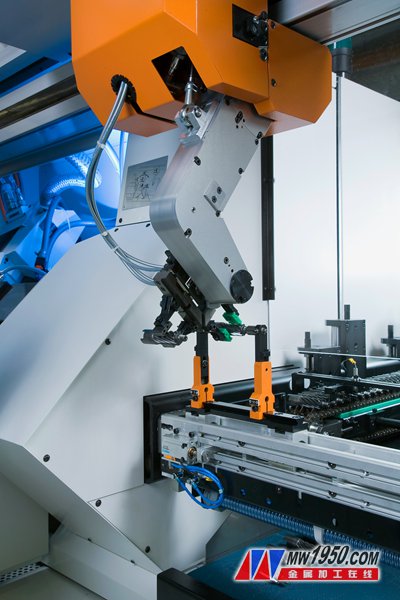
KOEPFER's experts have the technical advantage to reduce idle time by such a flexible loading door with double-rotating jaws.
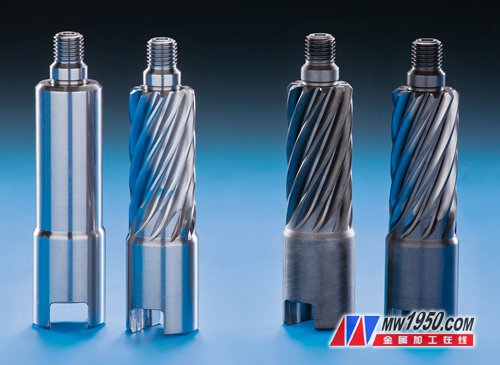
Steering gears are typical components of steering systems. This photo shows the workpiece after each machining stage, from turning, (soft) pre-milling, quenching to final shaving (hard).
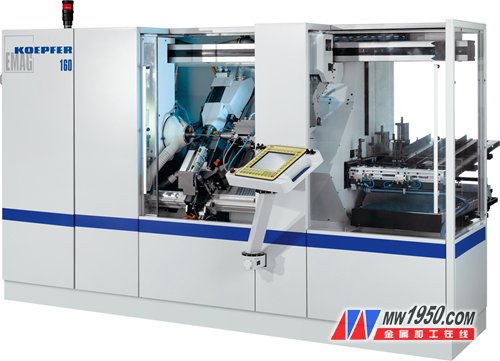
For toothed parts with a modulus of 2.5, the K160 is the fastest hobbing machine in the world. In addition to the extremely fast loading system, the machine is also equipped with a modern direct drive unit (on the cutting and spindle) and a user-friendly KOEPFER dialog programming control unit, which is very intuitive and convenient to use.
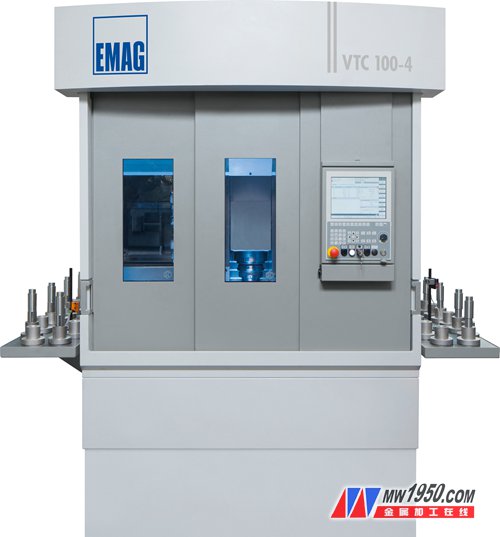
The VTC 100-4 is a 4-axis shaft-type workpiece lathe with a workpiece length of up to 400 mm and a diameter of 63 mm.
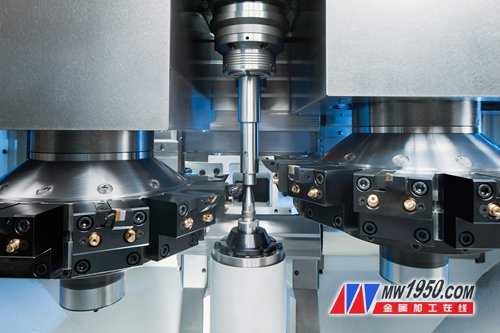
The turret of the VTC 100-4 is being loaded with the jaws. It picks up the workpiece from the side workpiece feed and places it in the spindle/tailstock.
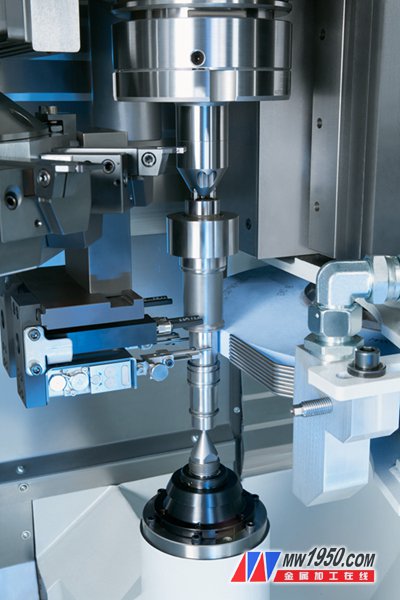
Machining area of ​​the VLC 100 GT: All precision machining processes (CBN grinding, hard turning and non-rolling turning) are done in one setup.
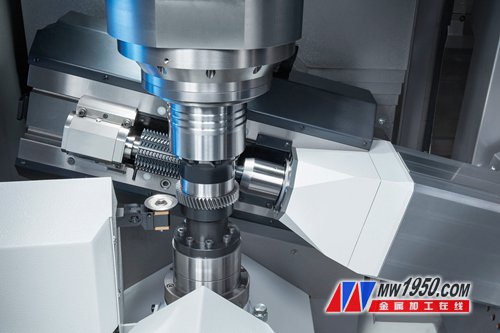
The VLC 200 H is designed for the machining of wheel-shaped workpieces with a diameter of 200 mm and a modulus of 4.
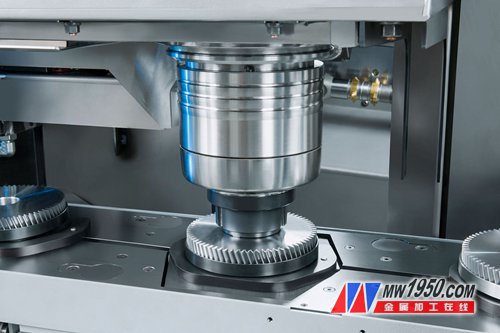
The VLC 200 H completes the loading and unloading process by picking up the spindle. Thanks to the EMAG's classic design, this intelligent system greatly increases the gear machining productivity of wheeled workpieces.
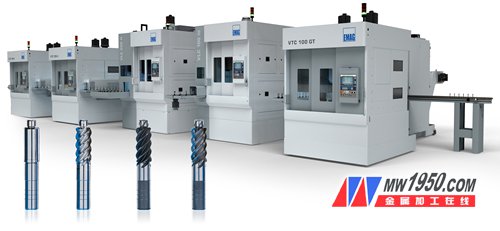
Steering gear production line
Stainless Steel Coil Tubes:
(1)Commodity name: Austenitic Stainless Steel Coil Tubes
(2)Process method: cold drawn/cold pilgered
(3)Material: TP304, TP304L,TP316, TP316L,dual grade 317L , 316Ti, TP321...DIN 17458 EN10216-5 TC1 1.4301 / 1.4307 / 1.4401 / 1.4404 ...
(4)Standard: ASTM ( ASME) ,EN, DIN, JIS and etc.
(5)Specifications: a) O.D.:1/4" -3/4"
b) W.T.:0.028"- 0.065"
c) Length:customized, max:1000m/pc.
(6)Delivery conditions: annealed & pickled
(7)Applications: widely used in petrol, chemical, pharmacy, foodstuff, machinery, spaceflight, war industry.
(8)boiler gas, hot water heating parts, hardware, shipping, power and other industries.
(9)Packing: packed by weaving bags, then protected by seaworthy wooden case.
Coil Tube,Steel Coil Tube,Seamless Weld Coiled Tube
YUHONG GROUP CO.,LIMITED , https://www.jessro-pipefittings.com