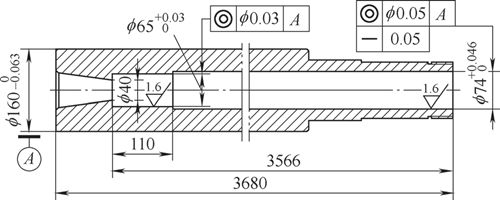
figure 1

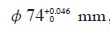
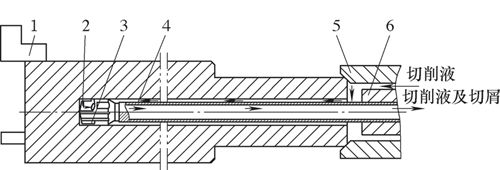
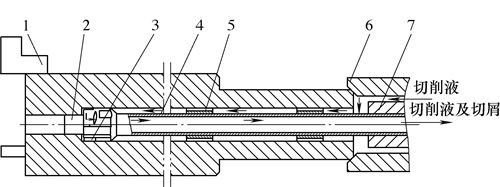
EVA Foam Animal is made from Eco-friendly, closed cell, non-smell and non-toxic Eva Foam material.
It consists of many different animal shape in EVA foam, which help baby to learn animals with small and safe toys.. You don't have to worry about it to be wet, cause the material is closed cell and antibacterial. Besides, when the puzzle is wet, it can just put on the wall, and won't fell, bringing a lot fun for children and baby when in bathroom.
Eva Foam Animal,Foam Animal Toys,Foam Animal,Foam Bath Toys,Eva Foam Animal Toys,Colorful Eva Foam Letters
Huizhou Melors Plastic Products Factory , https://www.melorsfoam.com